Historically speaking, fast food has been an industry willing to embrace change, automation, and innovation. The concept of creating and serving a consistent product efficiently is at the heart of every fast food chain’s ethos, and is what the consumer has come to expect across the world.
It should come as no surprise then that fast food restaurants are leading the way in embracing AI applications in the industry. This is particularly true when it comes to the two key performance indicators through which a fast food franchise or branch can be measured – consistency and efficiency.
One renowned pizza chain restaurant wanted to utilize AI technology in order to optimize its quality assurance procedures, and to ensure the brand’s standards were being met. Further to this, the pizza restaurant made this public, with the view of maintaining a level of transparency with its customers.
A second fast food restaurant wanted insight into the efficiency of its drive-thru system, and to establish ways that it could be improved, so also sought out AI solutions.
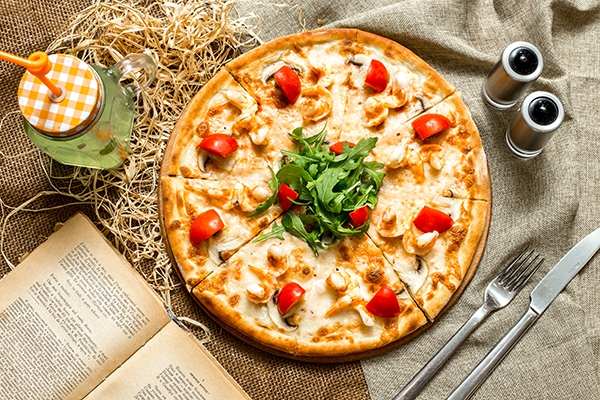
One of the biggest challenges in fast food is to ensure the service, aesthetic, and of course the food of each location conforms to the standards set by the brand as a whole. Therefore, the idea would be that to whichever location an individual goes, they can be certain that what they order reaches the standards they are accustomed to.
One problem however, is that this is not always possible at every location. While one franchise location may follow corporate guidance to the letter, another may be laxer with regard to producing the final product. Additionally, without regular quality assurance relating to the process, storage, ordering and overall standards of the food being served, an organization cannot fully evaluate the success of a given location, team, or employee’s performance.
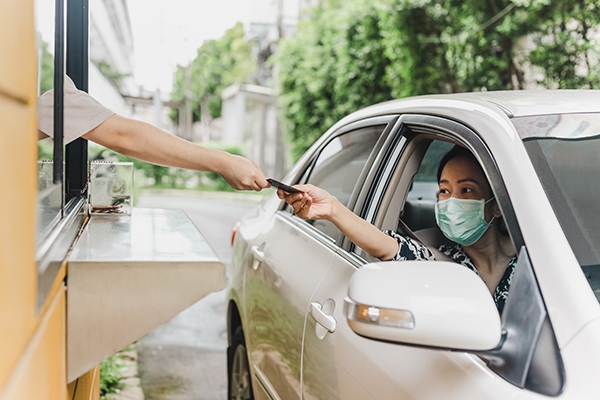
There are two big threats to a fast food restaurant’s efficiency, the organization of staffing, and the drive-thru. Where a location does not have enough staff, there will undoubtedly be longer waiting times for food, which can impact the restaurant’s performance and overall brand reputation. This is most clearly seen with respect to drive-thru bottlenecks.
In order to maintain efficient and fast service when operating the drive-thru, restaurants need information. This information takes many forms, such as inter-colleague communication between different work stations, but also an approximate time-based KPI to aim for to insure against long waiting lines and lost orders.
The renowned pizza chain restaurant introduced a food quality inspection application, powered by the BOXER-8233AI Compact Fanless Embedded BOX PC with NVIDIA® Jetson™ TX2 NX. This consisted of four high-resolution cameras which tracked each part of the pizza-making process, from ingredients being added, to its time in the oven, through to the quality assurance check prior to packaging.
By recording the pizza-making process via IP cameras, this data is not only available in real-time, but also transferred for later analysis using the built-in NVIDIA Jetson TX2 NX AI accelerator. Through AI inference training, the BOXER-8233AI will have effectively become the ‘eyes’ through which the software recognizes items that it has been trained to identify. This process enables the device to infer, based on the visual image whether a particular item is present or not.
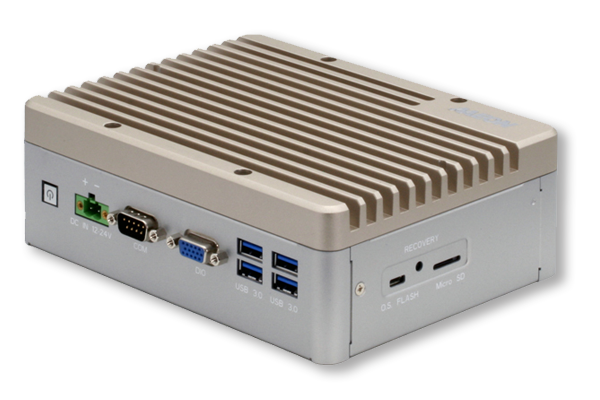
For example, during the first stage, the AI-trained software will detect whether or not there is a pizza. Secondly, it will identify the specific ingredients added, to ensure the ingredients and amounts are consistent with the order. It will then evaluate the finished product to ensure it conforms to the minimum standards to be delivered or served to the customer. While this is happening, the customer is also able to follow the process in real-time via an app.
The drive-thru restaurant employed a system to analyze the number of vehicles passing through the drive through lane at different times of the day, along with stock level analysis to understand rushes on particular menu items.
By using the BOXER-8221AI, the drive-thru restaurant was able to record real-time data on the number of cars waiting in line, the average time from order to service, and the number of sales lost due to bottlenecking. By using an IP camera as the ‘eye’ of the BOXER-8221AI, the visual data was analyzed in real-time using the computer’s AI accelerator, the NVIDIA Jetson Nano™. This combines the quad-core ARM® Cortex®-A57 MPCore processor with NVIDIA Maxwell™ GPU architecture featuring 128 NVIDIA CUDA® cores for incredible processing speed. It also means that multiple high-resolution images can be processed at the same time, which is exactly the type of specification the drive-thru restaurant required.
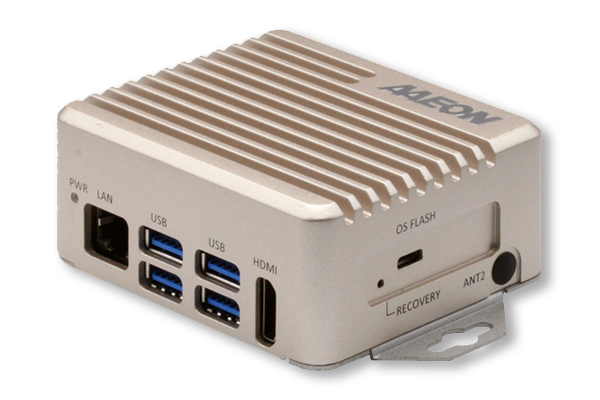
Because of the implementation of the BOXER-8233AI, the restaurant’s quality assurance measures became completely transparent to the customer, which has provoked positive press responses. Further to this, the restaurant was subsequently able to prevent lost sales and reduce the volume of food wasted through quality assurance failures.
In addition to this, the device provides meaningful management intelligence data to measure the performance of different staff members and teams. For example, the device enables management to measure the speed, efficiency, hygiene practices and accuracy of the pizza-making process throughout the day, and is able to discern the highest performing shift, along with highest performing workers.
The impact of the vehicle recognition application deployed at the fast food drive thru cannot be overstated. By recording real-time data on the number of cars waiting in line, the average time from order to service, and sales lost as a result of delays, the restaurant was able to better plan drive thru staffing needs.
Furthermore, having data that allows the restaurant to predict, and proactively plan for rushes on certain menu items also makes the stock and food preparation more efficient, and therefore less likely to run out of menu items, or to lose money through food waste.