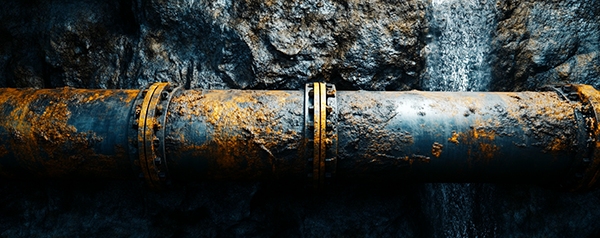
The 1960s saw enormous investment into the development of infrastructure worldwide, with millions of miles of underground piping literally laying the foundations for potable water distribution, sanitation, and sewage systems across multiple continents. However, as with anything built to such a scale, and despite the best laid plans of pipes and cement, this network of underground pipelines was not expected to last indefinitely. In fact, it was estimated at the time that the pipes installed would remain structurally sound for approximately 50 to 60 years, bringing us to the present day.
As the end of their expected effective lifespan approaches, the pipes installed decades ago now require inspection to evaluate key metrics, such as their remaining wall thickness, in order to evaluate their serviceability. Due to the complexity and spatial constraints of the task, one company responsible for evaluating the structural integrity of pipeline networks across multiple regions reached out to AAEON to find a product that could serve as the engine for a compact, rugged, mobile vehicle able to traverse and scan the pipes from within. Thankfully, AAEON was on hand with the PICO-MTU4, which fit both the technical and environmental specifications needed to make the project succeed.

Fitting components into extremely tight spaces
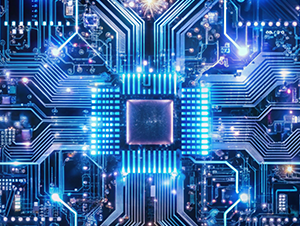
High processing power for edge analysis
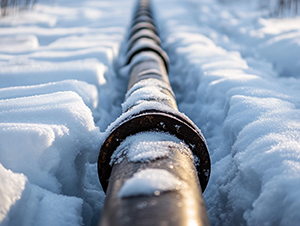
Vibration and temperature fluctuations in pipelines
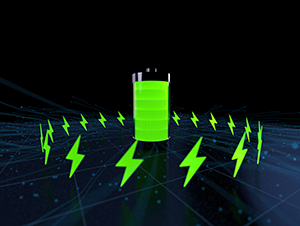
Minimizing energy consumption for long operation
There were a number of critical specifications needed from an embedded computer to ensure compatibility with the project. Given the solution would be deployed to examine pipes from the inside, all components needed to be incredibly small so as to fit into extremely tight spaces. Moreover, the need for advanced computing power–not only for data processing but also for the algorithmic analysis of that data on the edge–made this a particularly tall order.
The second major challenge came in finding a single board that could not only withstand the harsh deployment environment, but was reliable and efficient in operation. This meant that the board needed to be able to cope with environmental factors such as vibration from the vehicle’s vessel rotators and temperature fluctuations within the pipes. Additionally, it needed to be power efficient so as to allow for operational periods, thereby minimizing downtime for recharging. Given the scope of the project, this efficiency was a top priority; as multiple vehicles traversing millions of miles throughout a network of pipelines meant that every watt of power consumed would accumulate and prove costly, both literally and figuratively.
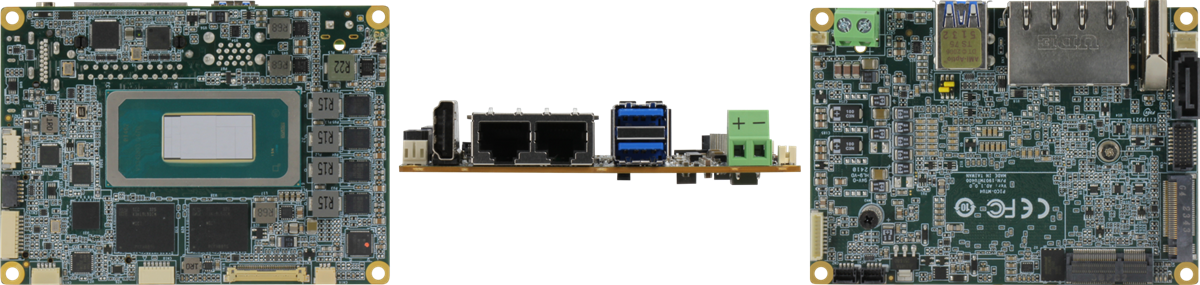
Upon receiving the project brief, AAEON knew that the PICO-MTU4 was likely the only product on the market capable of meeting all the requirements. The size constraints that disqualified the vast majority of embedded boards only highlighted the PICO-MTU4’s suitability, as its 100mm x 72mm form factor and lightweight design made it the perfect fit for the client’s miniature pipe scanner. Furthermore, the board’s minimal weight of just 0.08Kg meant that no excess weight would impede the efficiency and, consequently, the maximum operational longevity of the vehicle.
The board’s temperature tolerance range of -20°C to 70°C also served to protect against the temperature fluctuations that the solution may encounter. This is especially relevant considering that the depth of water line installation ranges from 12 inches below ground level—as well as at least 6 inches below the frost line—to several feet, depending on the region. At these depths, the board's ability to operate effectively below freezing point would prove invaluable.
Considering the vehicle was designed to maneuver through pipelines using vessel rotators, vibration was a potential area of concern. However, the PICO-MTU4 held the fortunate combination of soldered LPDDR5 system memory, an embedded SoC, and enough AI performance through its integrated Intel® Core™ Ultra NPU, eliminating the need for additional AI accelerator modules. The only components not fully onboard were the cameras and sensors used to gather data from within the pipes, which would ordinarily pose some risk of the cables connecting the board to the peripheral devices becoming loose. Fortunately, the PICO-MTU4 is available with lockable cables for its physical interfaces as an optional accessory, effectively addressing these concerns.
When undertaking the project, AAEON recognized the importance of selecting a product with a minimal energy footprint. Featuring the disaggregated die architecture of its Intel® Core™ Ultra SoC, the PICO-MTU4 not only provided exceptional efficiency but also maintained performance levels that are typically compromised in pursuit of energy savings. This combination of efficiency and performance made it the ideal solution for this challenging application. Below are the key advantages of the PICO-MTU4 that contributed to the project’s success:
PICO-MTU4’s Intel® Core™ Ultra SoC delivers remarkable energy efficiency through its advanced disaggregated die architecture. By reducing energy consumption while maintaining high levels of performance, it provided the ideal balance required for applications demanding prolonged operation without sacrificing computational power.
The board’s CPU handles resource allocation, multitasking, and data preprocessing, freeing up the integrated NPU for advanced AI tasks such as pose estimation and structural anomaly detection. With a power consumption of less than 0.01W, the NPU meets stringent ErP standards, reducing energy costs and eliminating the need for bulky external GPU modules, thus extending the operational range.
PICO-MTU4 excels in edge AI performance, enabling accurate detection of cracks, corrosion, and structural anomalies within pipelines. Its hybrid task distribution across the CPU, GPU, and NPU ensures real-time decision-making based on machine learning models, enhancing the system's ability to assess and respond to issues on the edge.
Equipped with lockable connectors, the board ensures secure and reliable data collection. Its USB interfaces support cameras for image data acquisition, while serial communication headers facilitate sensor installation. Complemented by soldered LPDDR5 memory, the board provides high-bandwidth, low-latency data transfer, remaining resistant to vibration and shocks while maintaining energy efficiency.
These features underline PICO-MTU4’s exceptional suitability for demanding environments, combining efficiency, durability, and advanced capabilities to meet the project’s complex requirements.
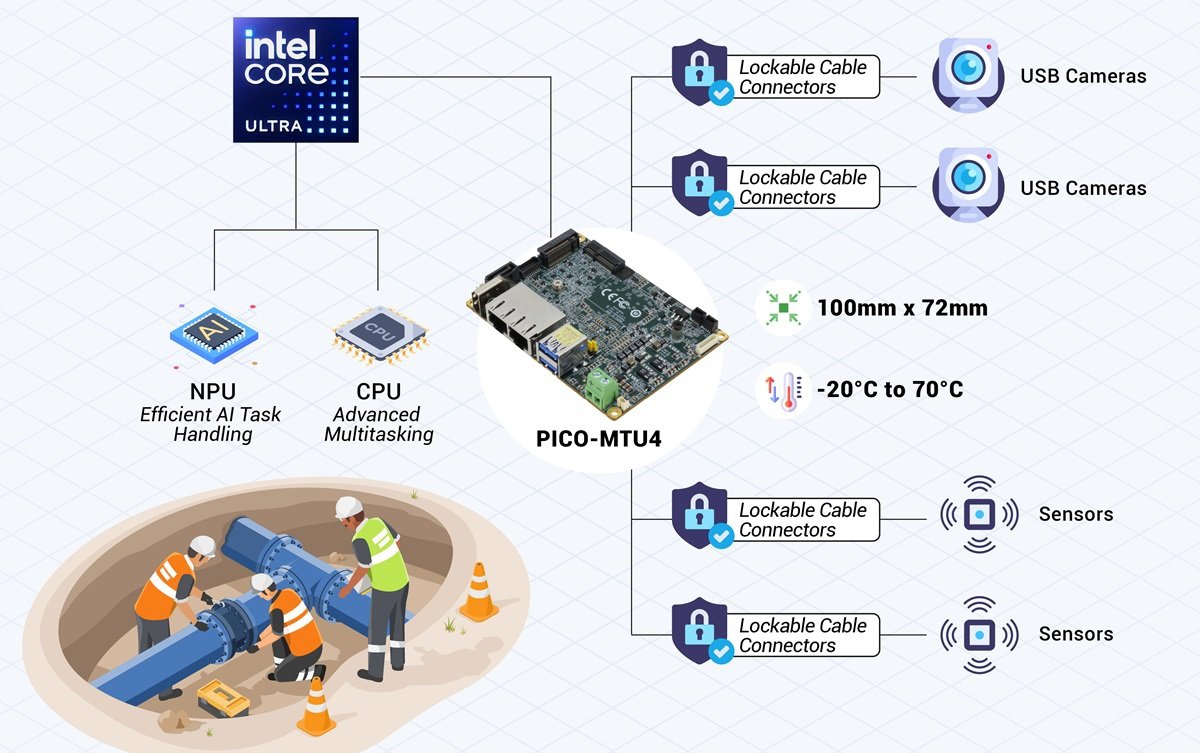
In successfully deploying the PICO-MTU4 in a project as complex and extensive as this, AAEON has illustrated the role that edge computing can play in modernizing aging infrastructure. With advantages stemming from its small form factor, hardware built for longevity in even the harshest environments, and an innovative blend of efficiency and edge computing performance, the PICO-MTU4 effectively enabled the development of a mobile vehicle capable of navigating the complex network of underground pipelines in need of monitoring.
This solution not only identified critical structural vulnerabilities in real time but also empowered operators to make data-driven maintenance decisions that have real-world consequences. The efficiency and precision offered by the PICO-MTU4 will extend the operational lifecycle of pipeline networks, reducing maintenance costs and turning the blueprints of last century into the foundations of the modern day.
With so much ground to cover, the PICO-MTU4 has kick-started a movement focused on modernizing essential infrastructure while minimizing environmental impact, thereby ensuring access to potable water and sanitation for future generations.